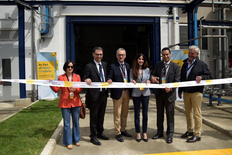
Facility Opening
Trinseo has inaugurated its polymethyl methacrylate (PMMA) depolymerization facility in Rho, Italy, on June 25. This pilot facility marks a significant advancement in the company's sustainability efforts.
Depolymerization Process
Depolymerization is a chemical recycling process that breaks down acrylic solutions into their constituent monomer, methyl methacrylate (MMA). This method allows for the recycling of PMMA sheets, which were previously non-recyclable through mechanical means. The process also removes additives and contaminants from pre- and post-consumer acrylic products, enabling more PMMA to be recycled.
Technological Advancements
The facility employs next-generation technology, utilizing an advanced continuous process to produce high-purity regenerated MMA. This technology is based on findings from the MMAtwo Consortium, a European Union-funded initiative under the Horizon 2020 research and innovation program. The goal is to create a new value chain for pre- and post-consumer PMMA and develop a versatile recycling process that reduces the carbon footprint compared to virgin MMA.
Applications
The recycled MMA (rMMA) produced at the facility is used in Trinseo’s ALTUGLAS™ and PLEXIGLAS® R-Life product lines. The high-purity rMMA is suitable for high-demand applications requiring excellent optical quality, such as vehicle taillights and caravan windows.