- The project has been funded by the Federal Ministry for Economic Affairs and Energy with around two million euros since November 1, 2020.
- The homogeneously catalyzed process reduces reaction temperature from 260°C to 130°C and pressure from 80 bar, eliminating 15% water by-product.
- The collaboration between CreativeQuantum and LIKAT began in 2017, with a patent application filed in 2018.
- The project aims to reduce production costs by using larger plants and catalyst quantities.
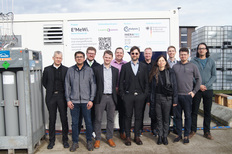
Project Overview
The E4MeWi research association is demonstrating efficient green methanol production at the Bitterfeld-Wolfen Chemical Park. The project compares two processes: INERATEC's heterogeneous-catalyzed direct synthesis and a new homogeneously catalyzed process by CreativeQuantum and the Leibniz Institute for Catalysis (LIKAT). The project has received around two million euros in funding from the Federal Ministry for Economic Affairs and Energy since November 1, 2020.
Innovative Processes
The homogeneously catalyzed process operates at significantly lower temperatures (130°C) and pressures, reducing the reaction temperature from 260°C and halving the required pressure of 80 bar. This process also eliminates the production of 15% water as a by-product, which simplifies the process by removing the need for energy-intensive separation. The synthesis gas for this process is derived from a new co-electrolysis method developed by Ruhr University Bochum.
Development and Collaboration
Since 2017, CreativeQuantum and LIKAT have focused on improving the catalytic system and process conditions, filing a patent application in 2018. The iterative development process was accelerated through quantum mechanical simulations and experiments. The Ruhr University Bochum team contributed by developing new materials for catalysis and advancing reactor development to the first high-performance cell.
Future Goals
The next major task is to reduce production costs by scaling up the plants and increasing catalyst quantities. The project aims to demonstrate the performance of both processes in an industrial environment and present their potential production costs. The integrated system was set up with support from local partners and the economic advisory board, including representatives from Linde, ThyssenKrupp, and Clariant.