- The upgraded 2A steam cracker now produces 15% more ethylene, propylene, C4, and pygas.
- Modifications included furnaces, compressors, column systems, tubes, and pipes.
- The 2A cracker is located at Shell's Rheinland refinery, Germany's largest.
- The site also produces methanol and converts feedstocks into various petrochemicals.
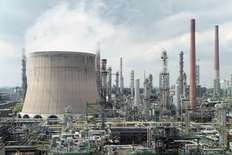
Investment and Upgrades
Shell Chemicals has completed significant investments at its Wesseling plant, enhancing energy efficiency and increasing production volumes. Key modifications were made to furnaces, compressors, column systems, tubes, and pipes, resulting in lower stack temperatures and reduced fuel consumption.
Increased Production
The upgraded 2A steam cracker now produces 15% more ethylene, propylene, C4, and pygas. This improvement aligns with Shell Chemicals' strategy to strengthen refining-chemicals integration and optimize feedstock positions at core manufacturing locations globally.
Strategic Location
In late 2011, Shell Chemicals rationalized its assets at the Wesseling site by closing the 2B cracker and focusing on increasing throughput and feedstock flexibility at the 2A cracker. The 2A cracker, which produces essential petrochemicals, is strategically located at Shell's Rheinland refinery, the largest in Germany. This location provides the cracker with advantaged feedstock and efficiently manages by-product streams.
Product Range
The steam cracker at Wesseling converts various feedstocks into ethylene, propylene, heavy olefins, and aromatic feeds for benzene and toluene production. Additionally, the site produces methanol. These chemicals are used in numerous end-products, including packaging, carrier bags, trash liners, injection molding, pipe extrusion, wire, and cable sheathing and insulation.