- Capacity for black synthetic iron oxide pigments increased by over 5,000 metric tons per year
- Pigments certified for use in ultra-high-strength concretes by an independent testing institute
- Production facility uses heat from the Laux process to create steam for subsequent steps
- LANXESS aims to be climate-neutral by 2040, reducing CO2 emissions by 50% by 2030
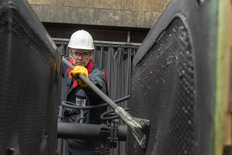
Capacity Expansion
LANXESS has expanded its production capacity for black synthetic iron oxide pigments at its Krefeld-Uerdingen site by over 5,000 metric tons annually. This expansion aims to meet the growing demand from the construction industry, particularly for coloring concrete.
Unique Production Process
LANXESS is the only global supplier producing these pigments using the Laux process. This method not only ensures high tinting strength and color consistency but also offers sustainability benefits. The pigments are certified for their high content of recycled raw materials by SCS Global Services.
Applications in Construction
The black pigments, Bayferrox 330 and Bayferrox 340, are preferred for high-quality cement-based building materials, including concrete paving stones and roof tiles. They are also certified for safe use in ultra-high-strength concretes (UHPC), which are essential for projects requiring high load capacities and lightweight structures.
Environmental Initiatives
The Krefeld-Uerdingen facility, the world’s largest for synthetic iron oxide pigments, uses the heat generated during the Laux process to create steam for subsequent steps, contributing to an excellent carbon footprint. LANXESS aims to further reduce its CO2 emissions, targeting climate neutrality by 2040 and a 50% reduction by 2030.