- The project, called Foam Recycling Ecosystem Evolution (FREE), will run for up to 24 months.
- Covestro's chemical recycling process recovers polyol and TDI precursor from PU foams.
- The project is half-funded by Ecomaison and coordinated by Covestro.
- A pilot plant for this process operates at Covestro's Leverkusen site.
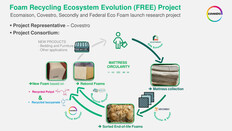
Project Overview
The Foam Recycling Ecosystem Evolution (FREE) project aims to create a new material cycle for flexible polyurethane (PU) foam from used mattresses. The initiative focuses on material efficiency and combines mechanical and chemical recycling technologies.
Key Partners
The project involves Ecomaison, Covestro, Secondly, and Federal Eco Foam. Ecomaison is dedicated to collecting and recycling used furniture, while Covestro provides advanced chemical recycling technology. Secondly specializes in dismantling and sorting, and Federal Eco Foam focuses on mechanical recycling of flexible foams.
Project Goals
The primary objective is to recycle sorted polyurethane foams as efficiently as possible. The partners aim to explore all possibilities in a future-oriented foam recycling ecosystem, leveraging both chemical and mechanical recycling methods.
Funding and Coordination
The project is coordinated by Covestro and is half-funded by Ecomaison. It is planned to run for a maximum of 24 months, with a focus on economic and ecological value co-creation.
Technological Advancements
Covestro has developed a unique chemical recycling process capable of recovering both main raw materials of flexible PU foams—polyol and the precursor to isocyanate TDI—in high purity. A pilot plant for this process operates at Covestro's Leverkusen site.
Future Outlook
The project aims to provide insights into the future of the foam recycling market. The partners believe that chemical and mechanical recycling can complement each other, given different specifications of inlet materials sorted at dismantlers.