- BASF and Stena Recycling aim to set up a battery recycling value chain for the European EV market.
- The focus is on recovering metals like lithium, nickel, and cobalt from end-of-life lithium-ion batteries.
- Stena Recycling will handle collection and pre-treatment in Halmstad, Sweden.
- BASF will refine and recycle the black mass in Schwarzheide, Germany.
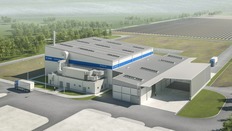
Partnership Overview
BASF and Stena Recycling have entered into a black mass purchase agreement to establish a battery recycling value chain for the European electric vehicle market. This collaboration aims to enhance black mass production processes to achieve high recovery rates for metals such as lithium, nickel, and cobalt, supporting closed-loop solutions for the industry.
Recycling Process
The recycling process begins with the collection, assessment, and pre-treatment of end-of-life lithium-ion batteries and battery production scrap. Stena Recycling will handle these initial steps, including the production of black mass through mechanical treatment in Halmstad, Sweden. The black mass, containing valuable metals, will then be processed at BASF’s prototype metal refinery in Schwarzheide, Germany.
Future Plans
BASF and Stena Recycling plan to scale this model to BASF’s planned commercial-scale battery recycling metal refinery in Europe. This initiative is part of a broader effort to support the electrification of society and promote a circular approach to battery production.
Environmental Impact
The use of recycled metals in new battery production significantly reduces the carbon footprint of batteries. Under this collaboration, Stena Recycling will manage the collection and pre-treatment of battery materials, while BASF will focus on recovering valuable metals and producing new cathode active materials for lithium-ion batteries.