- The Lysekil refinery conversion starts late 2024, producing 1.2 million cubic meters of renewable fuels annually.
- The project will cut fossil CO2 emissions by 2-3 million tons annually.
- Sanicro\u00ae 35 alloy is used for heat exchangers due to its corrosion resistance.
- Renewable fuels include Hydrotreated Vegetable Oil and Sustainable Aviation Fuel.
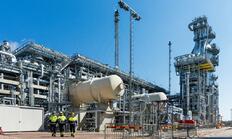
Project Overview
Alleima is supplying heat exchanger tubes for Preem's Lysekil refinery conversion from fossil to renewable fuels. This initiative is a significant part of Sweden's green energy transition, positioning Preem as the largest renewable jet fuel producer in northern Europe.
Timeline and Impact
The redevelopment of Preem's IsoCracker plant in Lysekil began in late 2024. Upon completion, it will produce 1.2 million cubic meters of renewable fuels annually, reducing fossil carbon dioxide emissions by 2-3 million tons each year. Concurrently, Preem will decrease fossil fuel production by an equivalent amount.
Technical Details
The transition involves replacing fossil raw materials with renewable ones, requiring advanced technology, particularly in the pre-treatment unit (PTU). The raw materials will undergo pre-treatment and purification at high temperatures before being used to produce renewable fuels like Hydrotreated Vegetable Oil (HVO) and Sustainable Aviation Fuel (SAF).
Material Challenges
Refinery processes demand robust materials, especially for renewable fuels, which often contain chlorides that can cause corrosion. Special materials are needed to withstand high temperatures and aggressive chemical environments. Group Coek, a heat exchanger manufacturer and long-time Alleima customer, secured the order with Preem.
Material Selection
Sanicro® 35 is used for the heat exchanger tubes, channels, and baffles due to its excellent corrosion resistance. Extensive lab tests with Preem confirmed that Sanicro® 35 can endure the extreme conditions of the pretreatment plant, offering a cost-effective alternative to more expensive nickel-based alloys.