- The plant used 30,000 tons of straw annually to produce 5.4 million liters of bio-ethanol.
- Operations began in December 2009 and shut down in 2015.
- The plant also produced 8,250 tons of biofuel and 11,000 tons of molasses.
- A fermentation protocol was tested in Skærbæk with a 93% yield.
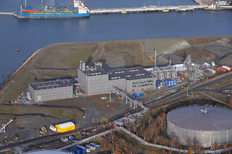
Project Overview
In collaboration with DONG Energy, ISC Consulting Engineers designed the Inbicon bio-ethanol plant in Kalundborg, Denmark. The plant focused on second-generation bio-ethanol production using agricultural and forestry remnants like wheat straw.
Design and Analysis
ISC Consulting Engineers handled the 3D piping design and produced all drawings for the upstream process using MicroStation PlantSpace. Triflex software was used for stress and flexibility analysis on critical steaming pipes, which operate under high pressure and temperature. Certification packages for authority approval were also managed by ISC.
Production Details
The plant processed 30,000 tons of straw annually, producing 5.4 million liters of bio-ethanol, which was mixed into gasoline at the Statoil Refinery in Kalundborg. Additionally, the plant produced 8,250 tons of biofuel and 11,000 tons of molasses for animal feed. Other products included 8,250 tons of ethanol, 13,100 tons of lignin pellets, and a natural bacteria inhibitor.
Operational Timeline
The plant began operations in December 2009, coinciding with the UN Climate Summit COP15 in Copenhagen. However, in autumn 2014, DONG's management decided to shut down the facility in 2015, halting the second planned demonstration campaign.
Fermentation Protocol Testing
Due to the shutdown, the semi-continuous fermentation protocol developed by Terranol was tested at the Inbicon GMO-approved pilot plant in Skærbæk. The protocol achieved a 93% yield in the refill test at a 300L scale using the Terranol yeast strain, cV-110.
Conference Presentation
Both Inbicon and Terranol presented their joint results at the “37th Symposium on Biotechnology for Fuels and Chemicals” in San Diego, USA, in April 2015, providing an excellent opportunity to share their findings.