- The BioPG plant converts glycerol into renewable propylene glycol, reducing CO2 by 60%.
- Air Liquide provided the license, engineering, and equipment, using BASF's technology.
- The plant has an annual capacity of 30,000 metric tons, meeting 75% of Poland's needs.
- BASF's catalyst has been in use for over a decade, ensuring high selectivity and efficiency.
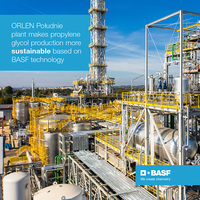
Introduction
ORLEN Południe has completed the first year of operation of its BioPG plant in Trzebinia, Poland. The plant converts glycerol, a by-product of biodiesel production, into renewable propylene glycol (BioPG).
Environmental Impact
BioPG, derived from glycerin, is a bio-based product used in various industries, including polyester resins, polyurethanes, paints, de-icing solutions, and food industry solvents. It reduces the CO2 footprint by at least 60% compared to fossil-based propylene glycol while maintaining the same quality.
Technology and Collaboration
Air Liquide Engineering & Construction provided the license, basic engineering, and proprietary equipment for the plant, utilizing BASF's technology. BASF’s BioPG technology has been operational at full scale for over a decade, demonstrating high selectivity and glycerol conversion with the H9-66 catalyst. This catalyst enables hydrogenation in the liquid phase without needing intermediate or solvent separation, resulting in lower energy consumption.
Production Capacity and Goals
The BioPG plant supports ORLEN Group’s objective of achieving CO2 neutrality by 2050. With an annual capacity of 30,000 metric tons, ORLEN Południe aims to meet 75% of Poland's propylene glycol needs, making it the first Polish producer of this chemical.