- Elite will supply post-use plastic to Mura's hydrothermal recycling facility in Teesside, operational by mid-2024.
- Mura's Hydro-PRT process converts waste into hydrocarbons for new plastic production.
- The process uses supercritical water for efficient recycling, reducing the need for fossil resources.
- A 2023 study showed Hydro-PRT saves 1.8t CO2 per tonne of plastic compared to incineration.
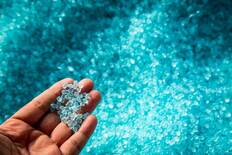
Partnership Announcement
Mura Technology has signed a feedstock supply contract with Elite Recycling Solutions. Elite will provide post-use plastic packaging to Mura's hydrothermal advanced recycling facility at Wilton International science park in Teesside, UK. The facility is in its final commissioning phase and is expected to start operations by mid-2024.
Hydro-PRT Process
Mura's Hydro-PRT process uses supercritical water to convert plastic waste into valuable hydrocarbon products. This method allows for the recycling of a wide range of plastics, including post-consumer packaging, and produces high yields of recycled hydrocarbons for new plastic manufacturing. The process can recycle the same material multiple times, significantly reducing the need for fossil resources in plastic production.
Environmental Impact
A 2023 independent Life Cycle Assessment (LCA) by Warwick Manufacturing Group (WMG) found that Hydro-PRT saves 1.8 tonnes of CO2 equivalent per tonne of plastic processed compared to incineration. This translates to an 80% reduction in carbon emissions, equivalent to 40,000 tonnes of CO2 annually from Mura's first site in Teesside.
Future Studies
A new study by WMG, set to be published in June 2024, evaluated the carbon impacts of combining advanced recycling with mechanical recycling. The study found a 42% reduction in carbon emissions compared to the current model of incineration and mechanical recycling, making incineration a less preferred option.