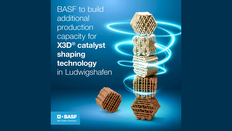
Investment in X3D Technology
BASF is set to increase its production capacity for X3D technology, an innovative additive manufacturing method for catalysts utilizing 3D printing. The new facility, located in Ludwigshafen, Germany, is projected to begin operations in 2026, producing catalysts on an industrial scale.
Advantages of X3D Catalysts
X3D technology marks a significant advancement in catalyst design and production. Catalysts created with this method are mechanically robust and feature an open structure, which reduces pressure drop across reactors and enhances surface area. These improvements lead to better catalyst performance, enabling customers to achieve higher efficiency, increased reactor output, improved product quality, and reduced energy consumption, aligning with green transformation goals.
Versatility and Customization
A key benefit of X3D technology is its versatility, applicable to a wide range of catalytic materials, including both precious and non-precious metal catalysts, as well as carriers. This flexibility allows for customization according to specific customer needs by adjusting parameters like infill patterns, fiber diameters, and orientations.
Proven Commercial Success
BASF has successfully operated commercial plants using X3D catalysts for several years, achieving notable results. The technology is positioned to influence both green and traditional value chains, offering enhanced efficiency and faster speed-to-market.