- The electrolyzer, built with Siemens Energy, can produce up to one metric ton of hydrogen per hour.
- Construction took around two years, with funding of €124.3 million, including €37.3 million from Rhineland-Palatinate.
- BASF invested approximately €25 million in the Hy4Chem project.
- Hydrogen is used in producing ammonia, methanol, and vitamins.
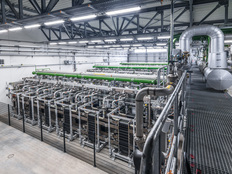
Project Overview
BASF has commissioned Germany's largest proton exchange membrane (PEM) electrolyzer at its Ludwigshafen site. The 54-megawatt electrolyzer is designed to produce zero-carbon hydrogen, supplying up to one metric ton per hour to the main plant. The project, developed in collaboration with Siemens Energy, integrates seamlessly into the site's production and infrastructure.
Environmental Impact
The electrolyzer has the potential to reduce greenhouse gas emissions at BASF's main plant by up to 72,000 metric tons annually. It uses electricity from renewable sources to produce hydrogen, which is then fed into the site's hydrogen Verbund network. This supports the production of chemical products with a reduced carbon footprint and contributes to the development of a hydrogen economy in the Rhine-Neckar Metropolitan Region.
Funding and Investment
The project received up to €124.3 million in funding, with €37.3 million provided by the Rhineland-Palatinate government. BASF invested around €25 million in the Hy4Chem project, which was selected as part of the IPCEI Hydrogen expression of interest procedure.
Hydrogen Applications
Hydrogen produced at the Ludwigshafen site is used in the production of ammonia, methanol, and vitamins. Previously, hydrogen was primarily produced through natural gas-based steam reforming or as a by-product. The new electrolyzer marks a significant step in transforming hydrogen production technology at the site.