- The Schwarzheide plant will create about 30 jobs and start in early 2024.
- Black mass production involves mechanical treatment of batteries to extract lithium, nickel, cobalt, and manganese.
- BASF plans to build a commercial hydrometallurgical refinery for battery recycling by mid-decade.
- Battery recycling helps meet EU policy requirements for recycling efficiency and material recovery.
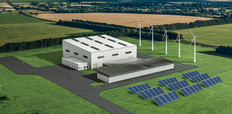
New Battery Recycling Plant
BASF is set to build a commercial-scale battery recycling black mass plant in Schwarzheide, Germany. This investment will enhance BASF’s cathode active materials (CAM) production and recycling hub in the region. The location is strategic due to the proximity of numerous EV car manufacturers and cell producers in Central Europe. The project is expected to create around 30 new production jobs, with operations commencing in early 2024.
Black Mass Production
Black mass production is the initial step in the battery recycling process, involving the mechanical treatment of batteries. The resulting black mass contains significant amounts of key metals such as lithium, nickel, cobalt, and manganese, which are essential for producing CAM. This black mass will serve as the feedstock for a commercial hydrometallurgical refinery that BASF plans to establish by mid-decade.
Environmental Impact
Battery recycling is crucial for reducing the CO2 footprint of battery electric vehicles and meeting the ambitious, circularity-driven policy requirements anticipated under the proposed EU Battery Regulation. These regulations will address the recycling efficiency of lithium-ion batteries and set targets for material recovery and recycled content for nickel, cobalt, and lithium.
Strategic Goals
With this investment, BASF aims to establish a full battery recycling value chain, optimizing the end-to-end recycling process and supporting a circular economy. This initiative will reduce dependency on mined raw materials and provide a closed-loop system from end-of-life batteries to new CAM production.